What are the classifications of screw lathes?
1, Short thread lathe
Short 1, short thread lathe
The layout of short thread lathes is basically similar to that of ordinary lathes. The thread formation movement between the workpiece and the tool is completed by the end CAM mounted in the middle of the bed instead of the lead screw. The lift profile of the CAM makes the tool holder advance and turn the thread. The drop profile returns the tool holder. It can avoid frequent positive and reverse rotation of the spindle and lead screw when high-speed thread turning on the general lathe.
2. Pipe screw lathe
The pipe screw lathe is generally provided with a large hole on the headstock, and the workpiece is gripped by two chucks at both ends of the spindle for rotating movement after passing through the hole. There are generally two ways to feed the tool: one is similar to the ordinary lathe by the lead screw to drive the slide and the tool holder in front of the bed; The other is achieved by the flat comb external thread cutting head (see automatic opening thread cutting head) on the slide located in the center of the bed into the workpiece and then move forward. Some machine tools for processing long pipes are also equipped with workpiece supports. The pipe thread lathe has been partly controlled by numbers. With each revolution of the workpiece, the tool moves evenly according to the number of feed pulses equivalent to the distance of the selected pitch, which is very convenient for machining taper threads, replacing the pitch and correcting the pitch error. This type of machine can process workpieces up to 15 meters long and up to 400 mm in diameter.
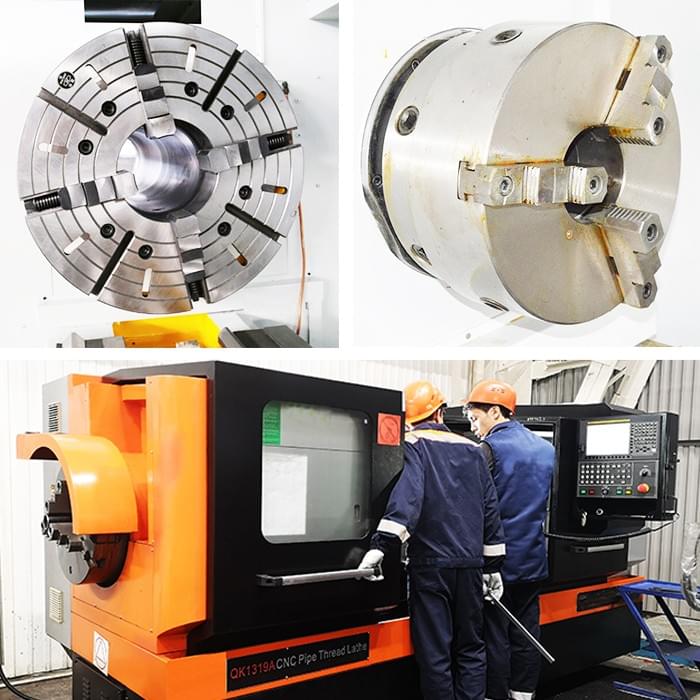
3. Tubing joint screw lathe
Tubing joint screw lathes can also be digitally controlled. Because the inner cone threads at both ends of the pipe joint are different in direction and have higher concentricity requirements, the workpiece chuck on some machine tools can be turned with the workpiece after processing one end of the thread by hydraulic method in order to turn the thread at the other end.
4. Lead screw lathe
The difference between the lead screw lathe and the ordinary lathe is that the lead screw has a large diameter and is placed between the two guide rails of the bed, rather than in front of the bed. In order to improve the machining accuracy, the machine tool is equipped with a pitch error correction device, which is mainly used for turning precision lead screws. The workpiece pitch error is generally not more than 7 microns per 300 mm. The layout of the screw lathe is basically similar to that of the ordinary lathe. The thread formation movement between the workpiece and the tool is completed by the end CAM mounted in the middle of the bed instead of the lead screw. The lift profile of the CAM makes the tool holder advance and turn the thread. The drop profile returns the tool holder. It can avoid frequent positive and reverse rotation of the spindle and lead screw when high-speed thread turning on the general lathe.
2. Pipe screw lathe
The pipe screw lathe is generally provided with a large hole on the headstock, and the workpiece is gripped by two chucks at both ends of the spindle for rotating movement after passing through the hole. There are generally two ways to feed the tool: one is similar to the ordinary lathe by the lead screw to drive the slide and the tool holder in front of the bed; The other is achieved by the flat comb external thread cutting head (see automatic opening thread cutting head) on the slide located in the center of the bed into the workpiece and then move forward. Some machine tools for processing long pipes are also equipped with workpiece supports. The pipe thread lathe has been partly controlled by numbers. With each revolution of the workpiece, the tool moves evenly according to the number of feed pulses equivalent to the distance of the selected pitch, which is very convenient for machining taper threads, replacing the pitch and correcting the pitch error. This type of machine can process workpieces up to 15 meters long and up to 400 mm in diameter.
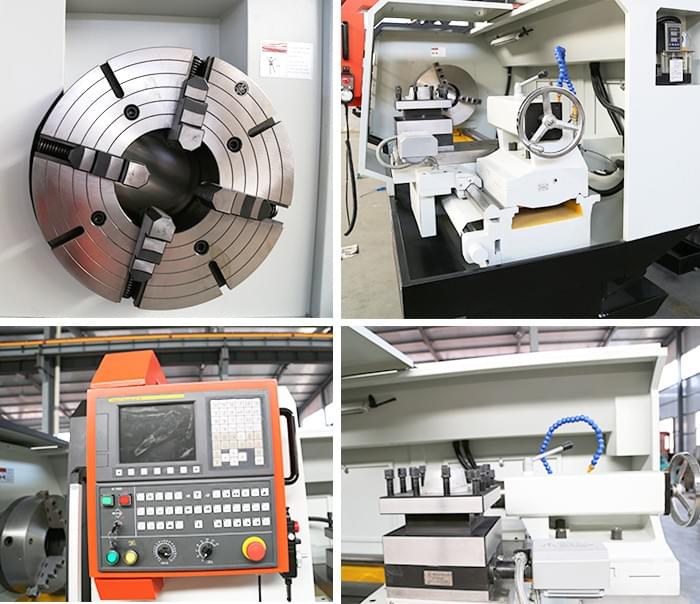
3. Tubing joint screw lathe
Tubing joint screw lathes can also be digitally controlled. Because the inner cone threads at both ends of the pipe joint are different in direction and have higher concentricity requirements, the workpiece chuck on some machine tools can be turned with the workpiece after processing one end of the thread by hydraulic method in order to turn the thread at the other end.
4. Lead screw lathe
The difference between the lead screw lathe and the ordinary lathe is that the lead screw has a large diameter and is placed between the two guide rails of the bed, rather than in front of the bed. In order to improve the machining accuracy, the machine tool is equipped with a pitch error correction device, which is mainly used for turning precision lead screws. The workpiece pitch error is generally not more than 7 microns per 300 mm.